Baubericht - Mini FW-190A (60cm)
Basis: FW-190 Version A4...
Die ausgewählte und auf Maß gebrachte 3-Seitenansicht als Papierschnitt...
...und im Vergleich die schon gebauten 60cm-Versionen der MiG-3 und Corsair
Rumpfbau
Der Rumpfkasten wird aufgezeichnet und ausgesägt... Dank der Bandsäge eine Sache von Minuten.
Dann wird geschnitten und die Form entsteht langsam...
Wie bekommt man die Cowling richtig rund? Genau - ein Rundloch sägen und den Styrodur-Rumpf etwas reindrehen...
...und weiter schneiden und schleifen.
Es folgt das Cockpit - Instrumententafel aus dem Netz + selbstgeschnitztem Sitz und Pilot.
Die Kabinenhaube wieder provisorisch aus Schrumpfschlauch gezogen und mit UHUpor aufgeklebt (so kann man sie später wieder abnehmen und ggfls. gegen eine tiefgezogene Haube tauschen)
Es folgt der Ausschnitt für die Motorplatte. Es wird ein AX-1806 (2.500kV) mit Frontmontage verbaut - die Motorplatte muss also entsprechend tief im Rumpf liegen, so dass der Motor eben mit dem Rumpf abschließt.
Leitwerke
Leitwerke sind gebaut (verstärkt mit Carbon und Balsa) und provisorisch in den Rumpf gesteckt.
Flächenbau...
Zum ersten Mal der Versuch, Flächen selbst zu schneiden. Dazu wurden Rand- und Wurzelprofile aus Alu gesägt und anschließend absolut glatt verschliffen. Der Draht darf beim Schneiden hernach nicht hängen bleiben. Die Profile werden auf eine Holzplatte mit genau der Spannweite der zu schneidenden Fläche geschraubt. Um eine linke und rechte Flächenhälfte herzustellen, müssen die beiden Profile getauscht werden. Da der Randbogen weniger Weg hat als die Wurzelrippe, sind auf die Schnittschablonen Markierungen von 1...10 aufgezeichnet. Am Besten schneidet man zu zweit: Der "Schnittmeister" an der Wurzelrippe gibt den Ton an. Er führt langsam den heißen Draht entlang der Aluschablone und liest dabei die Nummern ab - der Kollege an der Randrippe folgt in langsamerem Tempo Schritt für Schritt. Jegliche Ungleichmäßigkeit in der Schnittbewegung ergibt unwillkürlich eine Rattermarke auf der Fläche die anschließend gespachtelt und verschliffen werden muss!
Auf der Holzplatte sind kleine Nägel eingeschlagen - auf sie wird der auf die Spanweite abgelängte Styrodurblock gedrückt und arretiert. Dann beginnt der Schnitt.
Und so sieht nach 3 Fehlversuchen die erste Fläche aus. Ein klein bischen muss gespachtelt und geschliffen werden, aber mit etwas Übung wird das künftig sicher noch besser.
Rumpf, Flächen und Leitwerke sind eingeklebt, der Rumpfübergang angeformt und...
...der Motorspant sitzt fest.
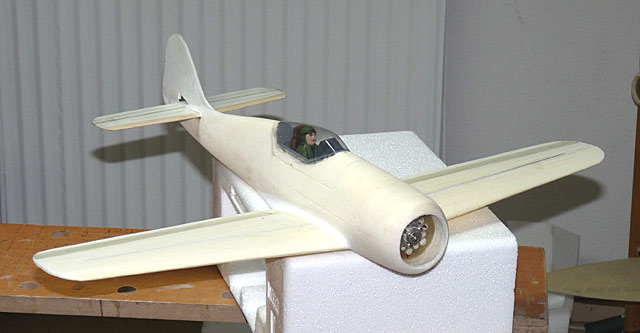
|